The bull-whip effect is a phenomenon that reflects increasing swings in inventory across the supply chain whenever there is a slight variation in consumer demand. It is a detrimental impact, experienced by companies around the globe, inducing inaccurate forecasts which usually end up in supply chain inefficiencies.
The Bull-whip Effect and its Causes
Companies often make forecasted demands of the amount of resources or stock they require in order to fulfill the customer needs efficiently i.e. without delaying orders or fiddling about. The fluctuations in customer demands often lead to amplified variations as we move up the supply chain driving companies to order more resources to meet the new expected demands. However forecasting errors and miscalculations induce the bullwhip-effect that flows up the supply chain leading to issues like time delays, increased cost and excess of inventory.
Bullwhip effect comes to surface due to factors associated with lead-time such as manufacturing delays, shipping delays and poor transmission of information across the supply chain. Human error and poor management also contribute to the bull-whip sting. Managers of companies are responsible for making decisions that affect the supply chain on many levels, from customer service to shipping of resources and whatnot. Many times these managers forecast trends in demand that negatively affect the supply chain contributing to the bull-whip phenomenon. This eventually leads to supply chain inefficiencies like lack of communication and coordination, forecasting demand errors, price fluctuations, inflated orders, errors in batch ordering etc.
Impact of Bull-whip sting on Inventory, Shipping time and Cost
Companies make predicted demands to maintain a practicable inventory but the fluctuations in supply chain caused by bull-whip effect leads to companies having either a superfluous inventory or insufficient inventory. Both the excess and shortfall of inventories as a result of exaggerated order demands is detrimental to a company’s finances. Excessive inventory increases the costs for a company and can often result in wasted resources when the customer demand subsides. On the contrary, lack of inventory leads to delays in orders, unavailability of products and poor customer services which can be equally expensive for a company.
Basically in order to lessen the risk of time delays in receiving orders from the manufacturers and transportation companies, businesses tend to order supersized levels of inventory. These superfluous orders increase the idle time of resources at ports as there is a delay in warehousing operations i.e. off-loading containers. The increased idle time of containers at congested ports also adds the demurrage charges that need to be paid by the company.
Furthermore after the delayed offloading, the company also has to pay additional cost for timely land transportation due to the tight truckload capacity at the congested ports. Thus the bull-whip sting leads to supply chain shortfalls such as buying and storage of excessive inventories, revenue loss, delayed transportation, unavailability of certain resources, poor customer service and escalated costs of products for consumers.
SiteTrax reducing the bull-whip sting
Keeping in mind the chaos induced in the pandemic years by the bull-whip effect, businesses are shifting to accurate and automated real-time information sharing across the supply chain. SiteTrax is the answer to those businesses who want to enable information sharing and provide complete visibility to all supply chain partners through faster asset tracking. By providing real-time inventory and shipment information, SiteTrax facilitates businesses to mitigate the chances of disordering and delays while transporting inventory as per their predicted patterns. By timely synthesis of information regarding shipments in demand and using inventory accuracy and yard automation, issues associated with bull-whip effect can be avoided.
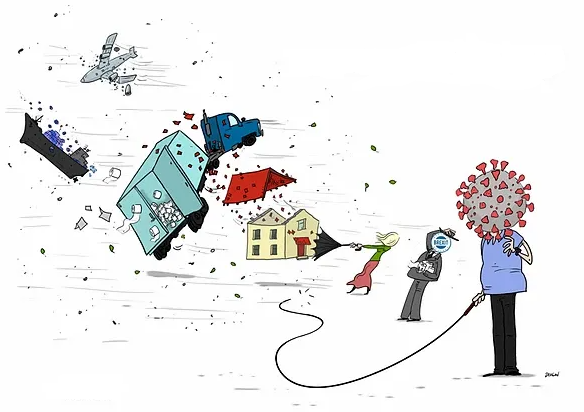
SiteTrax is an effective automation tool that can track container IDs in a couple of minutes using the SiteTrax mobile application. This application can gather important information, IDs as well as the GPS coordinates, of all assets resting in the container yard. This will eventually allow companies to operate more safely and productively as they can receive exact information regarding asset availability and can perform successful order batching. The GPS coordinates can be easily imported on google maps, block-chain disruptive ledgers and transportation management systems to do analytics and asset tracking efficiently. Warehousing operations are also improved as SiteTrax incorporation reduces container idle time in drayage, reducing any demurrage fee of companies who have their assets in the container yards.
SiteTrax is a solution to most logistic challenges including the bullwhip effect, eliminating supply chain inefficiency regarding excessive or insufficient inventory. Get SiteTrax today to build bridges between all stages of a supply chain and eradicate the bullwhip sting from causing any incompetence. Request a demo!